The Tools and Methods for Leading Quality
Providing customers with quality products while balancing reliability, innovation, and creativity can be difficult. Luckily, there are a few methods to ensure success.
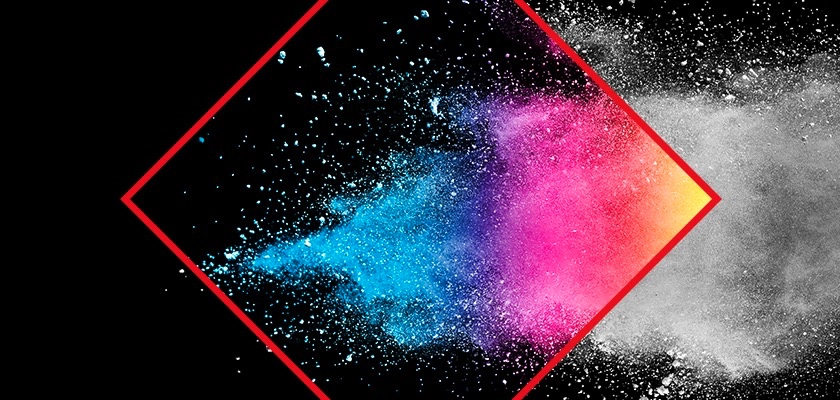
The quality movement is here to stay. Free markets and global competition combine to ensure competition for customers. Effective methods including Balanced Scorecard, Total Quality Management (TQM), Six Sigma, and others are being used to help organizations rise to the challenge.1
- Six Sigma Quality
One of the most important developments in quality management has been the introduction of statistical tools to analyze the causes of product defects in an approach called Six Sigma Quality. Originating at Motorola in 1986, Six Sigma became popular in the 1990s after it was embraced by General Electric. The term is now widely used to describe a variety of performance improvement efforts (improving quality, increasing efficiency, cutting costs, and the like).
In essence, Six Sigma seeks to remove variability from a process, thus avoiding errors and defects. Six Sigma quality is defined as having no more than 3.4 defects per million. At Six Sigma organizations, a product or service is defect-free 99.99966 percent of the time. The mantra of Six Sigma practitioners is DMAIC, standing for design, measure, analyze, improve, and control for quality excellence.2 - Lean Manufacturing
An increasingly popular approach to improving business performance is lean manufacturing, developed by Toyota as a way of achieving quality, flexibility, and cost-effectiveness. The essence of lean is commonsense management. It emphasizes the use of accurate data, insightful analysis, creative thinking to design work processes, the reliable measurement of important inputs and outputs, and the workforce discipline to do this without exception.
In a lean operation, rejects are unacceptable, overhead and inventory costs are kept to a minimum, and employees are empowered to halt production to correct problems at their source so that future problems can be avoided. With a well-managed lean process, an organization can develop, produce, and distribute products with significantly less staff, space, tools, time, and overall costs.3 - Checklist Procedures
Physician Atul Gawande has an interesting prescription: Every professional should write– in their field or out, for others or themselves, but by all means, write. Taking his own medicine, Gawande has written a trilogy of books on medicine today (Complications, Better, and The Checklist Manifesto). Gawanda's third book is a must-read for leaders challenged to get things done right, especially when tasks are complex and specialized knowledge and skills are required.
Gawande identifies the lowly checklist– well-conceived, communicated, and executed– as a tried-and-true answer that can be applied in the high-tech world of aviation, construction, finance, and medicine. This helpful book can be read from cover to cover and then applied in a customized way to achieve high-quality and reliable performance in any size or type of organization.4 - ISO Standards
The influence of the quality movement has become even more important with the emergence of ISO standards. ISO is a series of voluntary quality standards developed by the International Organization for Standardization, started in 1947. Headquartered in Geneva, Switzerland, ISO is a network of national standards institutions in more than 190 countries. Its purpose is to promote worldwide proprietary, industrial, and commercial standards. The number of companies receiving ISO certification continues to grow as hundreds of thousands of companies in manufacturing and service industries throughout the world are ISO certified. ISO 9001 standards of performance are set in eight areas:
- Customer Focus: Learning and addressing customer needs and expectations.
- Leadership: Establishing a vision and goals, establishing trust, and providing employees with the resources and inspiration to meet goals.
- Involvement of People: Establishing an environment in which employees understand their contribution, engage in problem-solving and acquire and share knowledge.
- Process Approach to Work: Defining the tasks needed to successfully carry out each process and assigning responsibility for them.
- System Approach to Management: Putting processes together into efficient systems that work together effectively.
- Continual Improvement: Teaching people how to identify areas for improvement and rewarding them for making improvements.
- Factual Approach to Decision Making: Gathering accurate performance data, sharing the data with employees, and using the data to make decisions.
- Mutually Beneficial Supplier Relationships: Working in a cooperative way with suppliers.5
Successful initiatives to improve quality performance share five characteristics: management commitment, employee buy-in, thorough training, daily execution of principles and practices, and positive reinforcement.
Evaluation
Rate your organization on a scale of 1-20 in each area:
- Management Commitment to Quality Products
- Employee Buy-in to Quality Processes
- Thorough Training for Quality Performance
- Daily Execution of Quality Principles and Practices
- Positive Reinforcement for Quality Results
Interpretation:
90-100 = A Excellent
80-89= B Very Good
70-79= C Average
60-69= D Poor
59-Lower= Failure
The leadership message is that quality performance is a never-ending quest and leaders set the pace.6
In One of America's Toughest CEO Jobs: Fixing PG&E, Katherine Blunt describes how CEO Patti Poppe surprised her board with a multibillion-dollar plan to bury the utility's fire-prone power lines. Bold action was needed to stabilize the company. PG&E is one of the few American companies ever to have been convicted of homicide, after pleading guilty to 84 counts of involuntary manslaughter for its role in igniting the 2018 Camp Fire that destroyed the town of Paradise, California. Poppe's plan is to spend as much as $20 billion to bury 10,000 miles of power lines to substantially reduce wildfire risk by safeguarding electric lines from making contact with trees. No U.S. utility has ever attempted such a plan, partly because of cost and engineering obstacles. PG&E's challenge is to rapidly improve the safety of an electrical system roughly the size of New England, a system that continues to ignite wildfires that kill people and reduce the trust of customers, regulators, and legislators. Patti Poppe isn't working alone as she enlists the support of the entire workforce and it's not a completed task. Similar leadership is required to ensure quality in any organization– large or small; public, private, or nonprofit.7
The challenge to leaders and organizations today is to maintain the predictability and reliability of current products and services while fostering innovation and creativity. Current success and future survival require mastering both ends of the quality spectrum. This is called avoiding the tyranny of the or and embracing the genius of the and. More academically, it is called organizational ambidexterity– being able to achieve multiple objectives at the same time. An example of organizational ambidexterity and business success is the story of Google, known for both innovation and reliability, stretch goals and incremental progress, core values and operational freedom, and big thinking and bold action.8 Google's X Lab is a means of fueling innovation, reminiscent of the famous Bell Laboratories.9
- J. O'Toole and E. Lawler, The New American Workplace (New York: Palgrave Macmillan, 2015); R. Kaplan and D. Norton, The Balanced Scorecard (Boston: Harvard Business School Press, 2000); and R. Kaplan and D. Norton, Alignment (Harvard Business School Press, 2006). See also Ken Snyder, Shingo Institute, John M. Huntsman School of Business, Utah State University.
- S. Minter, "Six Sigma's Growing Pains," Industry Week (May 2009), pp. 34-36; and M. George, The Lean Six Sigma Pocket Tool Book (New York: McGraw-Hill, 2004).
- J. Liker and J. Morgan, "The Toyota Way in Services," Academy of Management Perspectives 20, no. 2 (May 2000), pp. 5-20; R. Delbridge, "Workers under Lean Manufacturing," in D. Holman et al., The Essentials of the New Workplace (Chichester, UK: John Wiley, 2004), pp. 19-36; and M. Imai, Gemba Kaizen (New York: McGraw-Hill, 2012).
- A. Gawande, The Checklist Manifesto (New York: Henry Holt and Company, 2009).
- International Organization for Standardization, “ISO9000/ISO1400: Understand the Basics,” http://www.iso.org.
- J. Juran, Juran’s Quality Handbook, 6th ed. (New York: McGraw-Hill, 2010); and J. Liker, The Toyota Way (New York: McGraw-Hill, 2004).
- K. Blunt, (2021, November 5) “One of America’s Toughest CEO Jobs: Fixing PG&E,” The Wall Street Journal. Accessed from: https://www.wsj.com/articles/one-of-americas-toughest-ceo-jobs-fixing-pg-e-11636104601
- K. Auletta, Googled (New York: Penguin Press, 2009); G. Gibson and J. Birkinshaw, "The Antecedents, Consequences, and Mediating Role of Organizational Ambidexterity," Academy of Management Journal 47 (2004), pp. 209-26; and B. Hindo, "At 3M, a Struggle between Efficiency and Creativity," Business Week (June 2007).
- J. Gertner, The Idea Factory (New York: Penguin Group, 2012).